Best Overview to Preventing Weld Undercut: Tips and Techniques
Wiki Article
Understanding the Art of Welding: Just How to Avoid Undercut Welding Issues for Flawless Manufacture Outcomes
Effectiveness and accuracy are critical in the globe of welding, where also the least flaw can endanger the structural stability of a made item. One common difficulty that welders face is damaging, a defect that can deteriorate a weld joint and lead to costly rework. By comprehending the source of undercut welding and implementing efficient strategies to stop it, welders can raise their craft to brand-new degrees of quality (Preventing weld undercut). In the search of flawless construction outcomes, understanding the art of welding to stay clear of undercut issues is not simply a skill but a requirement for those pursuing excellence in their job.Comprehending Undercut Welding
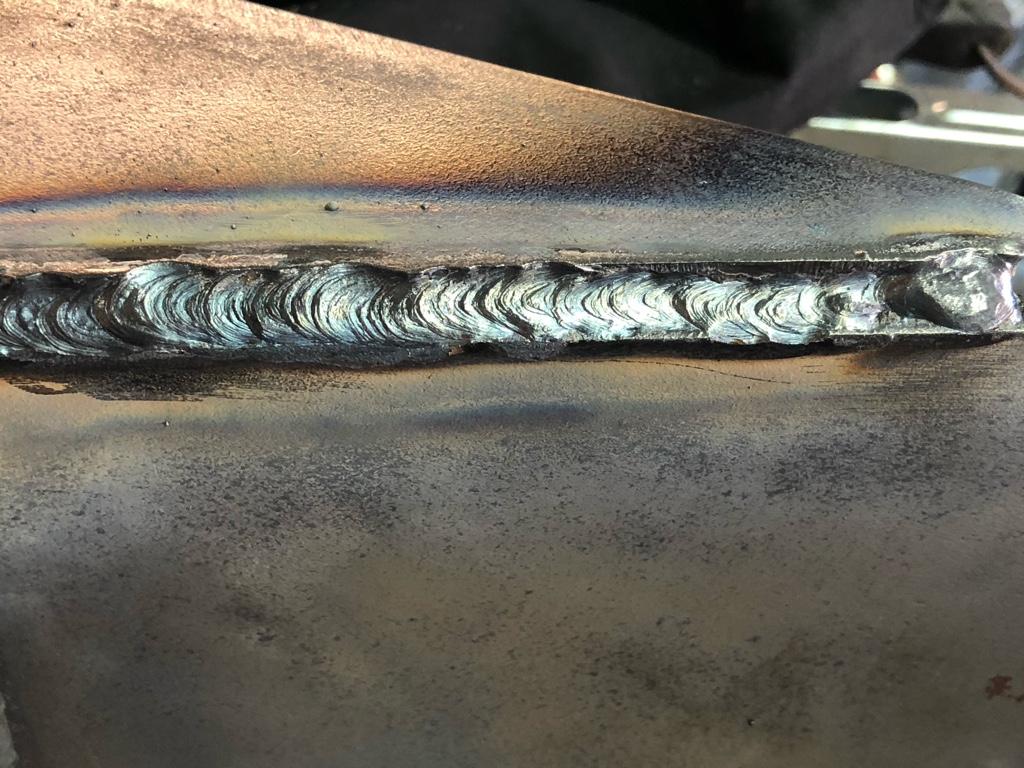
To avoid undercut welding, welders should make certain proper welding specifications, such as adjusting the present, voltage, travel speed, and keeping the right electrode angle. Additionally, utilizing the ideal welding technique for the certain joint arrangement is necessary. Using weaving motions or backstepping methods can aid ensure appropriate weld steel deposition and reduce the possibility of undercut development. Normal inspection of welds during and after the welding procedure is additionally crucial to catch any type of undercut very early and make essential adjustments to avoid further issues. Preventing weld undercut. By understanding the reasons of undercut welding and executing safety nets, welders can achieve top quality, structurally sound welds.
Sources Of Undercut in Welding
Recognizing the elements that add to damage in welding is important for welders to create premium, structurally audio welds. Undercutting occurs when the weld steel does not appropriately load the groove formed in between the base steel and the formerly deposited weld metal. A number of aspects can cause damage in welding. One typical reason is too much heat input. Welding at high temperatures for extensive periods can lead to the base steel melting greater than wanted, causing damage. Insufficient welding inaccurate or present welding speed can also contribute to undercut. Insufficient current may not provide enough warm to melt the base and filler steels effectively, while extreme rate can protect against correct combination, causing undercut. Furthermore, incorrect electrode angles or incorrect torch adjustment techniques can create locations of low weld metal deposition, promoting undercut. Comprehending these reasons and executing correct welding techniques can assist protect against undercutting concerns, making sure strong and durable welds.Techniques to avoid Undercutting

To minimize the risk of undercutting in welding, welders can employ strategic welding strategies aimed at boosting the quality and integrity of the weld joints. Furthermore, using the right welding strategy for the certain my response joint configuration, such as weave or stringer beads, can contribute to minimizing damaging.
Additionally, proper joint prep work, consisting of ensuring clean base products without contaminants and using the proper welding consumables, is essential in preventing undercut issues. Utilizing back-step welding methods and controlling the weld grain profile can additionally assist distribute warm evenly and lessen the threat of undercut. Normal assessment of the weld joint throughout and after welding, in addition to implementing quality control measures, can aid in finding and dealing with damaging concerns quickly. By executing these strategies faithfully, welders can attain remarkable manufacture results with minimal undercut issues.
Relevance of Proper Welding Specifications
Choosing and maintaining proper welding specifications is essential for attaining effective welds with very little flaws. Welding parameters refer to variables such as voltage, existing, take a trip rate, electrode angle, and shielding gas flow price that straight influence the welding procedure. These criteria need to be thoroughly readjusted based upon the kind of material being welded, its thickness, and the welding method employed.Correct welding specifications ensure the best amount of warm is put on thaw go right here the base steels and filler product evenly. If the parameters are set expensive, it can lead to extreme heat input, creating spatter, burn-through, or distortion. On the various other hand, if the parameters are as well low, insufficient blend, lack of infiltration, or damaging may take place.
High Quality Guarantee in Welding Operations

Final Thought
In verdict, understanding the art of welding requires a complete understanding of undercut welding, its causes, and techniques to stop it. By making certain correct welding criteria and applying quality control practices, flawless fabrication results can be achieved. It is vital for welders to consistently make every effort for excellence in their welding operations to prevent undercut problems and create premium welds.Undercut welding, a common issue in welding processes, happens when the weld steel does not effectively load the groove and leaves a groove or clinical depression along the bonded joint.To protect against undercut welding, welders must Discover More make sure appropriate welding specifications, such as readjusting the existing, voltage, travel rate, and keeping the appropriate electrode angle. Poor welding wrong or current welding rate can also contribute to damage.To alleviate the threat of undercutting in welding, welders can use critical welding strategies aimed at boosting the top quality and stability of the weld joints.In verdict, mastering the art of welding calls for a comprehensive understanding of undercut welding, its reasons, and methods to prevent it.
Report this wiki page